|
 |
 |
 |
 |
Расчетно-экспериментальный метод повышения ресурса УЭЦН |
 |
 |
 |
 |
 |
- Смирнов Н.И. к.т.н., с.н.с. Институт Машиноведения им.А.А.Благонравова РАН (ИМАШ РАН)
Смирнов Н.Н. ген.дир. ООО «ИМАШ ресурс»
- Ресурс установок электрических центробежных насосов (УЭЦН) в значительной степени влияет на производственные издержки при добыче нефти. Так затраты на текущий ремонт скважины в Западной Сибири составляет более 0,5 млн. рублей, а на капитальный ремонт скважины после аварии около 1,5 млн. рублей. По технологии эксплуатации УЭЦН – это электро-механическая система, функционирующая на отказ. Применявшиеся ОКБ БН в 80-е годы и развиваемые специалистами компании «НОВОМЕТ-ПЕРМЬ» [1] методы статистической теории надежности позволяют получить полезные результаты, например, прогнозировать вероятность наступления отказа при ограниченной выборке. Основным допущением является случайный характер отказа. Однако хорошо известно, что оборудование после эксплуатации зачастую сильно изношено, имеет поверхностные разрушения различного вида, т.е. налицо косвенные признаки возникновения постепенных отказов. Именно по этой причине большее значение имеют модели, базирующиеся на законах механики разрушения, учитывающие кинетику процессов разрушений различной физической природы (изнашивание, коррозия, усталость и т.п.). Основным признаком постепенного отказа является то, что вероятность его возникновения P(t) в течение заданного периода времени от t1 до t2 зависит от длительности предыдущей работы изделия t1.
Можно выделить основные виды отказов УЭЦН:
1. Отказы функционирования:
- отказ по критерию прочности, заключающийся в разрушении элементов корпуса или НКТ и падении нижней части установки на забой скважины. Применяющиеся жаргонные определения отказа – «полет», «РС-отказ»(расчленение самопрозвольное) не отражают физической сущности и некорректны в научном плане,
- отказ электрической системы (пробой кабеля, короткое замыкание в электродвигателе или разъеме), на практике определяемый как «R=0».
2. Параметрический отказ, заключающийся в недопустимом по техническим требованиям изменении выходных параметров (дебит, напор) установки.
Подъем оборудования вследствие геолого-технологических мероприятий нецелесообразно относить к категории отказа. На практике под отказом зачастую понимают причину отказа, например: износ, мехпримеси, солеотложения и т.д. Отсутствие общепринятых стандартизованных терминов надежности, единых подходов к анализу отказов и статистической информации по их причинам, незнание физики процессов разрушения приводит к тому, что при решении существующих и возникающих проблем надежности УЭЦН главным является рационализаторский подход.
Отказ по критерию прочности, который можно квалифицировать как аварию, в 90-е годы являлся, а в отдельных компаниях и сейчас является наиболее чувствительным аспектом надежности УЭЦН в силу больших затрат на капитальный ремонт скважин после аварии и отсутствия понятной теории, объясняющей его возникновение и методы его предотвращения.
Исследования по данной проблематике [2-6] основаны на качественных объяснениях отдельных процессов, протекающих в УЭЦН, либо количественной оценке предельного состояния механической системы с использованием упрощенных расчетных моделей.
Системный подход, развиваемый в ИМАШ РАН предполагает следующие этапы:
- разработка физической модели отказа на основе анализа статистических данных об эксплуатации оборудования и результатов исследования поверхности разрушения различными физическими методами;
- математическое моделирование условий наступления отказа, выявление ресурсоопределяющих узлов и деталей;
- разработка и внедрение ресурсных технологий.
На основе фрактографических иссле-дований разрушенных в процессе эксплуатации крепежных деталей, фланцев и других корпусных деталей установили [7,8], что наблюдаются два основных вида разрушения:
- под действием статических нагрузок, превышающих допустимые;
- при наличии нагрузок переменных по амплитуде и во времени.
Первый вид разрушения встречается при разрушении корпуса газосепаратора, вала, при срезании резьбы. В этом случае расчеты сводятся к проверке условия статической прочности nт>=[n]т [8,9], где запас прочности по пределу текучести nт=,бт/б определяется пределом текучести бт и наибольшими приведенными напряжениями б, соответствующими действующим на насос статическим нагрузкам. По условию статической прочности фланцево-болтовые соединения имеют более чем четырехкратный запас.
Второй вид разрушения представляет наибольший интерес и связан с динамикой установки, которая приводит к возникновению нагрузки с переменной амплитудой.
Для определения запаса прочности na при регулярном переменном нагружении можно воспользоваться известной зависимостью [10]

бзат- напряжение от усилия затяжки, бвн- напряжение от внешней нагрузки,
- предел выносливости при симметричном цикле нагружения,
- коэффициент, характеризующий чувствительность металла к асимметрии цикла.
- При использовании расчетной зависимости (1) необходимо учитывать два принципиально важных момента. Переменные напряжения, в общем носят стохастический характер и изменяются во времени. Для случая действия на установку сил с переменной во времени амплитудой при расчетах используют линейную гипотезу суммирования усталостных повреждений, что весьма серьезно усложняет расчеты. Более подробна эта методика изложена в работе [10].
Второй важный момент связан с пределом выносливости. Реальные условия эксплуатации характеризуются наличием жидкости в области возникновения и развития усталостной трещины. Поэтому необходимо использовать понятие ограниченного предела выносливости. Структура зависимости (1) показывает, что необходимо знать величину напряжений от внешней нагрузки бвн и оценить степень изменения величины напряжений от усилия затяжки бзат в процессе спуско-подъемных операций и эксплуатации УЭЦН.
-
Математическая модель динамики насоса
Исследование динамических характеристик УЭЦН производили с помощью конечно – элементного пакета MSС/NASTRAN, v70,5. Область моделирования включает в себя всю установку и участок НКТ длиной 17 м. Наиболее подробно моделировались секции насоса. Степень детализации выбрана такой, чтобы была возможность учесть взаимодействия между валом и каждым направляющим аппаратом. Учитывали влияние гироскопических эффектов при регулярной круговой прецессии путем приложения дополнительного динамического изгибающего момента, действующего со стороны рабочего колеса на вал при прецессионном движении.
Принципиальным отличием данной модели является то, что учитывали износ пар трения. Эта задача решалась в предположении, что:
- между втулками защитными вала и направляющими аппаратами при возникновении контакта имеется большая, но конечная контактная жесткость, контактирующие поверхности локально цилиндрические,
- зазор между втулками защитными вала и направляющими аппаратами изменяется в соответствии с выбранной моделью износа
dh/dt = kfFtan, где:
dh/dt – скорость изнашивания радиальных опор,
Ftan=fFrad – тангенциальная сила в паре трения,
f – коэффициент трения,
Frad – радиальная сила в паре трения
- дисбаланс рабочих колес распределен по длине насоса и величине случайным образом с максимальным значением 0,01Н на радиус, что соответствует величине эксцентриситета 2,8х10-4 м. Рассматривались также наиболее интересные случаи однонаправленного на определенной длине распределения дисбаланса,
- начальную величину исходного зазора принимали одинаковой для всех ступеней и равной 10-4м. Хотя в общем случае указанные зазоры также распределены по случайному закону,
- величину коэффициента трения в парах трения принимали равной 0,02. Это значение характерно для граничного режима смазки.
В процессе моделирования задавали разные величины жесткостей при контакте корпуса УЭЦН с обсадной колонной, учитывали изгиб корпуса насоса из-за кривизны обсадной колонны и другие нагружающие параметры.
Сложность состояла главным образом в том, что вал насоса установки вращается в длинном ряде кольцевых зазоров между втулками защитными и направляющими аппаратами, их контакт под действием центробежных сил происходит с соответствующим изменением жесткости системы. Задача определения формы деформированной оси вала при необходимости учитывать условия совместности перемещений примерно в 400-ах парах является конструктивно и геометрически нелинейной задачей, «утяжеленной» конечно – элементной реализацией модели. Указанную проблему решали путем применения процедур прямого нелинейного расчета системы на динамическое воздействие с использованием нелинейных контактных элементов, позволяющих моделировать контакт вала с втулкой и направляющего аппарата при учете переменной жесткости контакта и величины радиального зазора.
Разработанная конечно – элементная модель динамики УЭЦН позволяет определить типы движения вала насоса, влияющие на форму износа пар трения.
Явление прямой несинхронной прецессии вала насоса УЭЦН, рис.1, является сильно нелинейным процессом.
Наличие низкочастотных прецессионных движений существенно осложняет динамику всей системы: в районе f=10Гц имеется достаточно плотный собственный спектр.
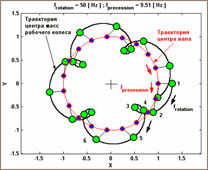
Рис.1 Схематическое изображение прецессионного движения одного сечения вала насоса (несинхронная прецессия). С другой стороны вся конструкция сильно задемпфирована и находится в далеко закритичной области работы. Синхронная прецессия вала, рис.2, связана с однонаправленным распределением дисбалансов вдоль оси насоса вследствие износа и малым уровнем демпфирования в системе.
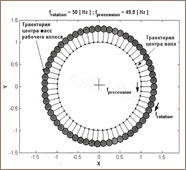
Рис.2 Схематическое изображение прецессионного движения одного сечения вала насоса (синхронная прецессия).
Величины изгибающих моментов растут пропорционально износу радиальных пар трения для всех типов распределений дисбалансов и величин износостойкости, рис.3.
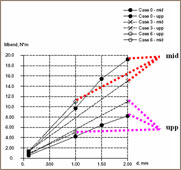
Рис.3 Эволюция величин изгибающих моментов по мере износа между двумя секциями насоса – индекс mid, и в области ловильной головки – индекс upp.
Износ радиальных подшипников во времени изменяется экспоненциально без насыщения, рис.4.
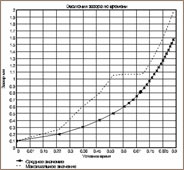
Рис. 4 Износ радиальных подшипников во времени
Разработанная модель позволяет определить напряженно – деформированное состояние деталей и узлов УЭЦН при различных видах движения вала, условиях эксплуатации для оценки вероятности наступления отказа по критерию прочности («полет»), рис.5.
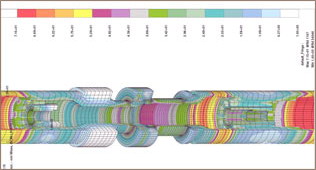
Рис.5 Иллюстрация возможностей применения разработанных компьютерных методов для моделирования динамики роторной системы и исследования напряженно-деформированного состояния узлов УЭЦН в процессе эксплуатации
Проверку и идентификацию математической модели УЭЦН проводили с помощью специального экспериментального стенда для испытаний рабочей ступени. Его принципиальным отличием является вал переменной жесткости, позволяющий задавать ту или иную форму движения рабочего колеса и исследовать процесс динамики ступени при изнашивании в абразивосодержащей среде.
На основании математического моделирования получены величины напряжений в опасных сечениях корпуса, выявлено, что имеются условия возникновения не только синхронной прецессии с частотой 50Гц, но может возникать асинхронная прецессия с частотой порядка 10Гц. Каждому виду прецессии соответствует своя форма износа пары трения «втулка защитная – направляющий аппарат».
При синхронной прецессии вала происходит одностороннее изнашивание втулки защитной или ступицы рабочего колеса и равномерное по окружности изнашивание отверстия направляющего аппарата. Асинхронная прецессия характеризуется равномерным износом обоих контактирующих поверхностей. Необходимо заметить, что бытующее мнение у некоторых авторов [2] относительно влияния кривизны скважины на формирование одностороннего износа втулок защитных является в определенном смысле заблуждением. При изгибе корпуса насоса в обсадной колонне силы в опорах, возникающие вследствие изгиба, действуют со стороны направляющих аппаратов на вал. Поэтому защитные втулки должны изнашиваться равномерно, а отверстие направляющего аппарата – с одной стороны, стороны действия силы. Это наблюдается в начальные моменты времени, когда идет приработка. Но при дальнейшем изнашивании реализуется один из видов прецессии вала и соответствующая форма износа.
Доказано, что отсутствуют условия возникновения резонанса системы, а вероятность наступления отказа по критерию прочности в значительной степени определяется неблагоприятным сочетанием различных факторов: распределением дисбалансов рабочих колес, величиной износа радиальных пар трения, величиной затяжки, накопленными повреждениями у вторично используемых деталей и т.д.
Этот вывод имеет принципиальное значение для выработки мер борьбы с отказом по критерию прочности, т.к. ставит под сомнение эффективность использования различных антирезонансных устройств, гасителей [4], устройств для предотвращения отказов [11] и т.д. Все вышеперечисленное давно не используется в передовых нефтяных компаниях по причине отсутствия, прежде всего, практического смысла и низкой надежности. Математическое моделирование позволяет утверждать, что снижение числа отказов по критерию прочности можно достичь за счет точного нормирования определяющих характеристик: прочностных, износовых, динамических, технологии изготовления и эксплуатации.
В табл.1 приведена оценка влияния эксплуатационных, конструкторско-техноло-гических факторов на напряженное состояние деталей при усталостном характере разрушения.
Эксплуатационные, конструкторско – технологические факторы |
Степень влияния фактора на напряженное состояние |
Неуравновешенность вращающихся масс (дисбаланс, солеотложения в каналах рабочих колес и т.д.) |
Увеличивается амплитуда цикла ба |
Износ радиальных опор (втулка защитная вала, бурт рабочего колеса) |
Увеличивается амплитуда цикла ба |
Кривизна скважины, скорость опускания насоса в скважину |
Снижается жесткость стыка, уменьшается затяжка болтов бзат. Может произойти раскрытие стыка. |
Динамический уровень |
Изменяется среднее напряжение цикла бm |
Влияние пластовой жидкости |
Происходит дополнительное снижение предела выносливости за счет коррозии поверхности детали |
Нарушение технологической дисциплины при сборке фланцевых соединений, ненормированная затяжка |
Снижается надежность фланцево – болтовых соединений за счет перераспределения нагрузки |
Технологический брак при изготовлении, неправильное проектирование |
Снижение предела выносливости деталей за счет дополнительных концентраторов напряжений |
Кислотно – щелочные свойства перекачиваемой среды, наличие газа и мехпримесей. |
Коррозионно – механическое разрушение внутренней поверхности корпуса газосепаратора. Возможно дополнительное кавитационно – абразивное воздействие |
-
Проведение усталостных испытаний
Как видно из формулы (1) очень значимым резервом повышения запаса усталостной прочности является предел выносливости крепежных и фланцевых деталей. Как показали проведенные нами многочисленные усталостные испытания крепежных деталей и фланцево-болтовых соединений в сборе [8,9], для предотвращения отказов по критерию прочности одним из наиболее эффективных методов является применение разработанной ресурсной технологии изготовления деталей с целью получения высоких значений предела выносливости и циклической долговечности. Так, если серийный крепеж имеет предел выносливости 47МПа, то ресурсный (изготовитель ООО «ИМАШ ресурс») свыше 97МПа. Примечательно, что предел прочности в обоих случаях соответствует классу 10.9. Широкое применение ресурсного крепежа и модернизированных концевых деталей в нефтяных компаниях привело к резкому снижению отказов по критерию прочности по наиболее слабому элементу (фланцево-болтовому соединению) до малозначимых величин, рис.6.
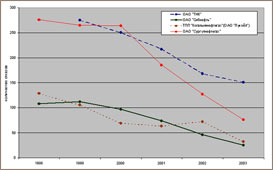
Рис.6 Динамика отказов по критерию прочности УЭЦН («полет») в результате применения ресурсных технологий.
Для входного контроля крепежа на выносливость при нагрузках с переменной амплитудой была разработана методика ИМАШ-059.01*, которая применяется на заводах-изготовителях УЭЦН и нефтяных компаниях.
В данной статье не приведены результаты исследования износа пар трения, который также определяет динамику насоса, что надеемся сделать в одной из следующих публикаций.
Авторы благодарны за содействие в работе к.т.н. Гринбергу В.А. и д.т.н., проф. Гуськову А.М.
Литература.
1. Перельман О.М. и др. Статистический анализ надежности погружных насосных установок в реальных условиях эксплуатации. // НИСОНГ. – 2003, №3 – с.28-34.
2. Дарищев В.И. и др. Комплекс работ по исследованию и снижению частоты самопроизвольных расчленений (РС – отказов) скважинных насосных установок, М.: ВНИИОЭНГ , 2000 – 84 с.
3. Уразаков К.Р. и др. Особенности насосной добычи нефти на месторождениях Западной Сибири. М.: ВНИИОЭНГ, 1997, 56с.
4. Пчелинцев Ю.В. Полеты насосов. – М.: ОАО «ВНИИОЭНГ», 2003. – 392с.
5. Перельман О.М., Пещеренко С.Н., Рабинович А.И. Нефтедобывающие насосы: динамика роторов и эксплутационная надежность// 2 Международная научно – техническая конференция “СИНТ’03” г.Воронеж, 15-20 сентября 2003г.
6. Волков В.Н. Новые исследования РС – отказов УЭЦН// НИСОНГ, 2003, №4
7. Смирнов Н.И. и др. Исследования и пути повышения ресурса УЭЦН //Химическое и нефтегазовое машиностроение, 2000, №3, с. 13-16.
8. Смирнов Н.И., Смирнов Н.Н. Прочность и износостойкость насосов (расчет, испытания, технология) // Материалы IX Всероссийской технической конференции «Производство и эксплуатация УЭЦН», г.Альметьевск, 1-4 ноября 2000 г.
9. Смирнов Н.И., Смирнов Н.Н., Мухамадеев К.Г. Исследования и пути повышения ресурса работы некоторых элементов УЭЦН // Материалы VIII Всероссийской технической конференции «Производство и эксплуатация УЭЦН», г.Альметьевск, 2-4 ноября 1999 г.
10. Когаев В.П. Расчеты на прочность при напряжениях, переменных во времени М., «Машиностроение», 1990г., 386 с.
11. Бочарников В.Ф., Пахаруков Ю.В. Вибрации и разрушения в погружных центробежных электронасосах для добычи нефти. – Тюмень: ТюмГНГУ, 2005 – с.141
|
 |
 |
 |
 |
|
|